Investment Casting Process Steps at China Casting Company
The following steps are what we follow to produce investment parts with complex geometries and intricate details.
1. Create wax pattern: A pattern that replicates the finished part geometry is made using one of two primary methods:
A. Build a wax injection die B. 3D print pattern I. If a wax injection die will be used, the first step involves designing and building a metal die from Aluminum. This die creates a wax replica of the desired part by injecting melted wax under high pressure into the cavity. The die can be made as a simple one cavity manual tool or a complex multi-cavity automatic tool depending on volume requirements. II. If a 3D printed pattern will be used, a CAD model which contains the part geometry is sent to a printer and the part is printed. 2. Wax Assembly: Next, the wax patterns are assembled onto runners and into a finished tree which is ready to be dipped. 3. Slurry Coating: The assembly is then dipped into a high-grade ceramic slurry to build a ceramic shell around the wax tree. 4. Stuccoing: After the slurry coating is done, particles of sand are dropped onto the surface of the wet tree assembly. This helps to thicken and strengthen the layer of coating on the wax assembly surface. 5. Repeat Steps 5 and 6: Repeat steps 5 and 6 until the assembly achieves the desired shell thickness. The assembly is then allowed to set and dry. 6. Dewaxing: The wax inside the newly built shell is now removed. Dewaxing is done using a steam-dewaxing autoclave or flash fire furnace. 7. Casting: Now the desired molten metal is poured into the pre-heated mold cavity. 8. Cooling: The mold then sits to allow the molten metal to cool and solidify which then becomes the final casting. 9. Shell Removal: The shell material is then removed through processes hammer knockout, vibration, and steel grit blasting. 10. Cut Off: The finished parts are then cut free from the gating and runner system. 11. Finishing: Various finishing techniques are then employed including grinding, sand blasting and coating to achieve the final surface needed. 12. Testing: Once the finishing operations are done, the parts are inspected for surface and sub-surface defects. Visual and fluorescent penetrant inspection is done for surfaces and X-ray is employed for sub-surface defect identification.
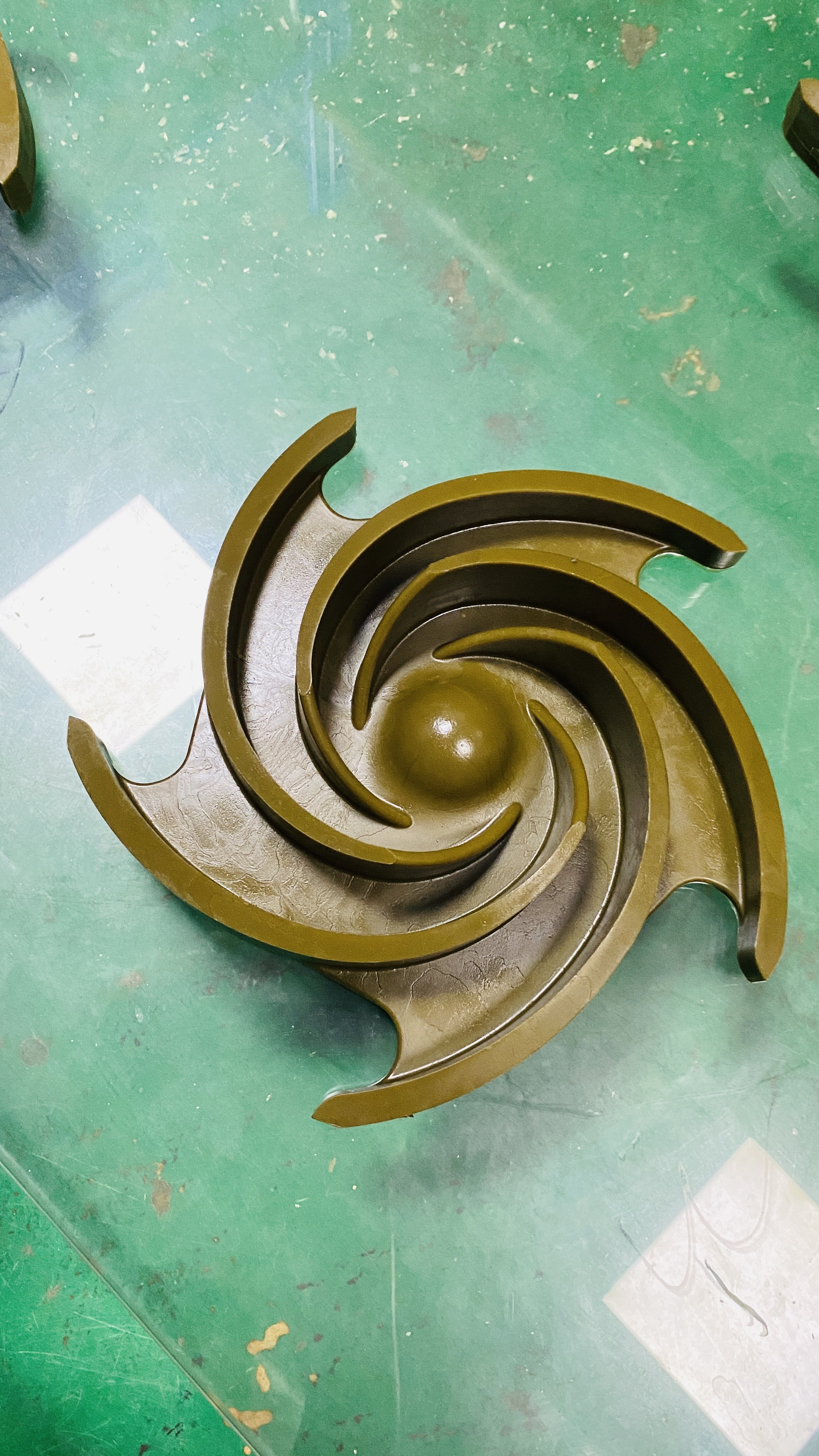